The production of Miscanthus pellets has gained popularity as a sustainable and renewable energy source. However, understanding the production costs associated with a Miscanthus pellet mill is crucial for producers to ensure profitability and sustainability. This article outlines the key components involved in calculating the production costs of a Miscanthus pellet mill, providing a comprehensive overview for potential investors and operators.
1. Understanding the Key Cost Components
When calculating the production costs of a Miscanthus pellet mill, several key components must be considered:
- Raw Material Costs: The cost of Miscanthus as a feedstock is one of the most significant expenses. This includes the costs associated with growing, harvesting, and transporting the Miscanthus to the pellet mill.
- Operational Costs: These costs encompass the day-to-day expenses of running the pellet mill, including labor, maintenance, utilities, and consumables.
- Capital Costs: The initial investment in equipment, machinery, and infrastructure is a crucial factor in determining overall production costs. This includes the cost of the pellet mill itself, as well as any additional equipment needed for processing, such as crushers and dryers.
- Overhead Costs: These are indirect costs associated with running the business, such as administrative expenses, insurance, and facility maintenance.
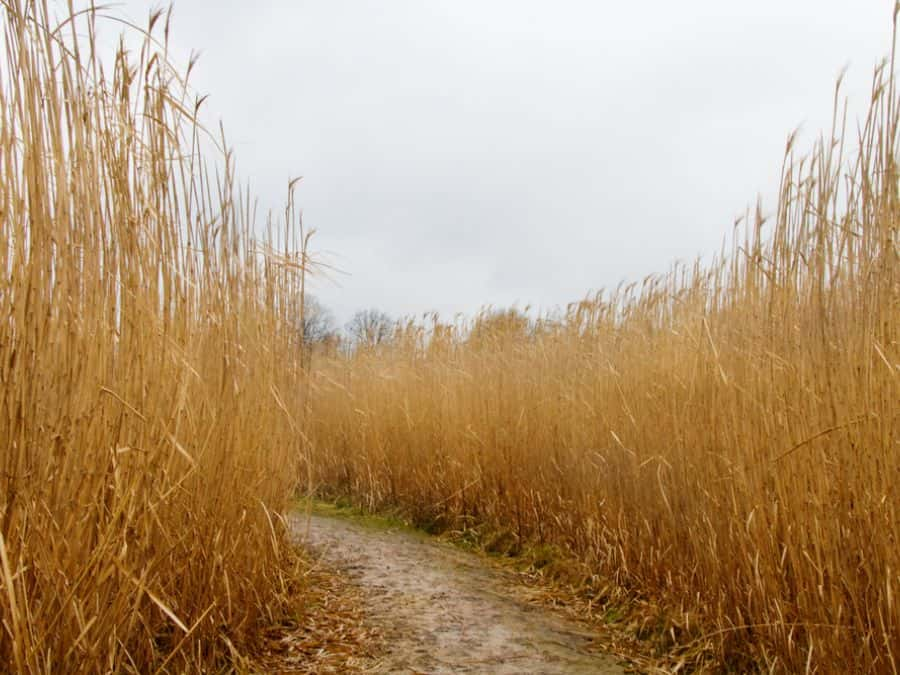
2. Calculating Raw Material Costs
The first step in calculating production costs is determining the raw material costs associated with Miscanthus:
- Cultivation Costs: This includes expenses related to land preparation, planting, fertilization, pest control, and harvesting. According to various studies, the cultivation cost of Miscanthus can vary significantly based on local agricultural practices and conditions.
- Harvesting and Transport: After harvesting, the Miscanthus must be transported to the pellet mill. This involves costs related to labor, equipment, and fuel. Calculating the distance from the field to the mill and the associated transportation costs is essential.
- Cost per Ton: To determine the total raw material cost, calculate the cost per ton of Miscanthus and multiply it by the amount needed for production. For example, if the cost is $50 per ton and 100 tons are required, the total raw material cost would be $5,000.
3. Estimating Operational Costs
Operational costs are ongoing expenses that must be accounted for in the production cost calculation:
- Labor Costs: This includes wages for operators, maintenance staff, and any administrative personnel. Calculate the total labor hours required for production and multiply by the hourly wage.
- Maintenance Costs: Regular maintenance is essential for ensuring the longevity and efficiency of the pellet mill. Estimate the annual maintenance costs based on historical data or industry standards. A common rule of thumb is to allocate around 2-10% of the initial equipment cost for maintenance annually.
- Utilities: The pellet production process requires energy for machinery operation, heating, and cooling. Calculate the average monthly utility costs (electricity, water, etc.) and annualize them for the production cost calculation.
- Consumables: This includes costs for lubricants, cleaning supplies, and any other materials needed for the operation of the pellet mill. Estimate these costs based on historical usage or industry benchmarks.
4. Assessing Capital Costs
Capital costs are significant investments that need to be amortized over the lifespan of the equipment:
- Equipment Costs: Determine the total cost of the pellet mill and any auxiliary equipment (e.g., crushers, dryers). This includes purchase price, installation, and any financing costs.
- Depreciation: To calculate the annual depreciation of the equipment, use methods such as straight-line depreciation. For example, if a pellet mill costs $100,000 and has a lifespan of 10 years, the annual depreciation would be $10,000.
- Financing Costs: If the equipment is financed, include interest payments as part of the capital costs. Calculate the total interest paid over the financing period and allocate it to the annual production costs.
5. Calculating Overhead Costs
Overhead costs are indirect expenses that contribute to the overall operation of the pellet mill:
- Administrative Expenses: This includes salaries for management, office supplies, and other administrative costs. Estimate these costs based on the organizational structure and operational needs.
- Insurance: Calculate the insurance costs for the facility and equipment. This is often based on the value of the assets and the type of coverage required.
- Facility Maintenance: Include costs for maintaining the production facility, such as repairs, cleaning, and utilities not directly associated with production.
6. Total Production Cost Calculation
Once all the individual components have been assessed, the total production cost can be calculated:
- Raw Material Costs: Total raw material cost (e.g., $5,000)
- Operational Costs: Total operational costs (e.g., labor + maintenance + utilities + consumables)
- Capital Costs: Annualized capital costs (e.g., depreciation + financing costs)
- Overhead Costs: Total overhead costs (e.g., administrative + insurance + facility maintenance)
Total Production Cost = Raw Material Costs + Operational Costs + Capital Costs + Overhead Costs
7. Cost Per Ton of Pellets
To determine the cost per ton of pellets produced, divide the total production cost by the total number of tons produced in a given period:Cost Per Ton = Total Production Cost / Total Tons Produced
8. Conclusion
Calculating the production costs of a Miscanthus pellet mill requires a comprehensive understanding of various cost components, including raw materials, operational expenses, capital costs, and overhead. By accurately assessing these factors, producers can gain valuable insights into their production efficiency and profitability.Understanding the production costs not only helps in pricing strategies but also aids in identifying areas for cost reduction and operational improvements. (Related post: grass pellet machine)
As the demand for renewable energy sources continues to grow, effective cost management will be essential for the sustainability and competitiveness of biomass pellet production. By focusing on accurate cost calculations, producers can better position themselves in the market and contribute to a more sustainable future.