Producing high-quality chicken feed is essential for poultry farmers aiming to maximize growth rates, improve health, and enhance overall productivity. To achieve this, specialized animal feed manufacturing machines are required to process various ingredients into nutritious and palatable feed. This article discusses the key machines suitable for producing chicken feed, focusing on their functions, benefits, and considerations.
1. Raw Material Handling Equipment
Efficient raw material handling is the first step in the feed production process:
- Silos: Silos are crucial for storing bulk raw materials such as corn, soybean meal, and other ingredients. They help maintain the quality of feed components and facilitate easy access for processing.
- Screw Conveyors: These machines transport raw materials from storage silos to the processing area. They are efficient and can handle various types of feed ingredients, ensuring a smooth flow of materials.
- Weighing and Batching Systems: Accurate measurement of raw materials is vital for ensuring the correct formulation of chicken feed. Automated batching systems weigh and mix ingredients according to specific recipes, ensuring consistency in the final product.
2. Grinding Machines
Grinding is a critical process that reduces raw materials into smaller particles, enhancing the digestibility of the feed:
- Hammer Mill: A hammer mill is commonly used to grind grains and other ingredients into fine particles. For chicken feed production, a hammer mill with a capacity of 30-55 kW is typically used. This machine ensures uniform particle size, which is essential for optimal feed efficiency and nutrient absorption.
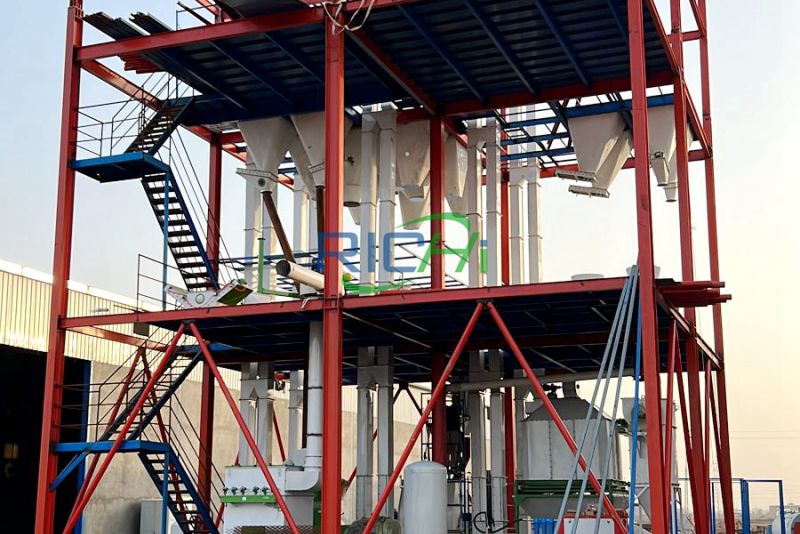
3. Mixing Equipment
Once the raw materials are ground, they need to be mixed thoroughly to ensure a homogeneous feed blend:
- Feed Mixer: A paddle mixer or ribbon mixer is used to combine the ground ingredients uniformly. A single roller double paddle mixer with an 11 kW motor is suitable for this purpose. Proper mixing ensures that all nutrients, vitamins, and minerals are evenly distributed throughout the feed, promoting optimal health and productivity in chickens.
4. Pelletizing Machines
The pelleting process is essential for transforming the mixed feed into pellets that are easy for chickens to consume:
- Pellet Mill: A pellet mill is crucial for compressing the mixed feed into pellets. A 55 kW feed pellet making machine is typically used for producing chicken feed pellets. The pellet mill compresses the feed mixture through a die, resulting in uniform pellets that enhance feed intake and reduce waste.
- Conditioner: Before pelleting, a conditioner is used to add steam and moisture to the feed mixture. This process improves pellet quality and durability, ensuring that the pellets hold their shape during storage and feeding.
5. Cooling and Screening Equipment
After pelleting, the feed pellets need to be cooled and screened to ensure quality:
- Counter-Flow Cooler: A counter-flow cooler is used to reduce the temperature of the hot pellets after they exit the pellet mill. This cooling process is essential for maintaining the quality of the feed and preventing spoilage.
- Vibrating Screen: A vibrating screen separates the cooled pellets by size, removing any fines or oversized pellets. This step ensures that the final product meets the desired specifications for chicken feed.
6. Packaging Machines
The final step in the production process is packaging the finished feed for storage and distribution:
- Packing Machine: A packing machine is used to bag the screened pellets into appropriate packaging, such as 25 kg or 50 kg bags. This equipment ensures accurate weighing and sealing of the bags, facilitating easy handling and transportation.
7. Dust Collection System
To maintain a clean and safe working environment, a dust collection system is essential:
- Dust Collector: A dust collector captures airborne dust generated during the grinding and pelleting processes. This system helps improve air quality and reduce the risk of fire hazards, ensuring a safer working environment for employees.
8. Control and Automation Systems
Modern feed production facilities often incorporate advanced control and automation systems to enhance efficiency:
- PLC Control Center: A programmable logic controller (PLC) manages and monitors the entire production process, allowing operators to control and adjust parameters as needed for optimal performance.
- Sensors and Monitors: These devices track critical parameters such as temperature, moisture, and flow rates, ensuring that the production process remains efficient and consistent.
Conclusion
Producing high-quality chicken feed requires specialized animal feed making machines that can handle the unique characteristics of the ingredients involved. From raw material handling and grinding to mixing, pelleting, cooling, screening, and packaging, each piece of equipment plays a critical role in ensuring that the final product meets the nutritional needs of chickens.When selecting machines for chicken feed production, factors such as capacity, raw material compatibility, efficiency, customization options, and maintenance support should be carefully considered. By investing in the right equipment and following best practices in feed manufacturing, poultry farmers can ensure a consistent supply of nutritious and palatable feed for their chickens, ultimately leading to improved growth rates, health, and profitability.As the demand for high-quality poultry products continues to rise, the importance of efficient and effective feed production cannot be overstated. By leveraging the capabilities of modern animal feed manufacturing machines, chicken producers can optimize their operations, reduce costs, and contribute to the sustainable growth of the poultry industry.