Introduction
With the rising demand for sustainable agricultural inputs and the growing emphasis on environmental protection, establishing an organic fertilizer production line with an annual capacity of 20,000 tons has become an attractive investment. Such a facility is considered medium-sized and suitable for regions with intensive farming or livestock activities. However, proper planning, engineering design, and execution are essential to ensure profitability, compliance, and long-term operational efficiency.
This guide walks you through the step-by-step process of designing a complete organic fertilizer production line with a 20,000-ton/year capacity, covering everything from feasibility analysis and site selection to equipment configuration and process flow design.
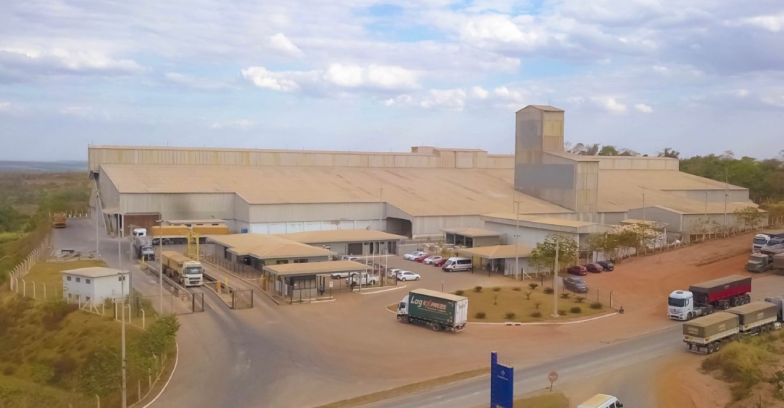
1. Market Analysis and Feasibility Study
Before initiating the design process, conduct a detailed feasibility study to assess the market demand, competition, raw material availability, and regulatory environment.
Key Factors to Analyze:
- Demand for organic fertilizer in the target region
- Type of crops and soil conditions in local agriculture
- Volume and type of organic waste (e.g., cow dung, chicken manure, food waste, crop residues)
- Local environmental regulations
- Pricing trends and ROI forecast
Output:
A business plan that outlines expected revenue, operational costs, and payback period (usually 2–4 years for a 20,000 TPA plant).
2. Raw Material and Nutrient Composition Planning
A 20,000-ton/year organic fertilizer line will need approximately:
- 40,000–60,000 tons of raw organic materials annually, assuming 30–50% moisture reduction during processing.
Common Raw Materials:
- Livestock manure (cow, pig, chicken, goat)
- Agricultural residues (straw, husks)
- Food waste and green waste
- Municipal sludge (if permitted)
- Additives: peat, zeolite, microbes, humic acid
Nutrient Goals: Typical organic fertilizer should contain:
- ≥ 45% organic matter
- NPK: 3-5% (can be enriched if needed)
- pH 6.5–8
- Pathogen and weed seed-free (Related post: 9-10T/H Organic Fertilizer Processing Plant In Iraq )
3. Site Selection and Layout Planning
Ideal Site Size: 5,000–8,000 square meters
Key Location Factors:
- Near raw material sources (farms, slaughterhouses, markets)
- Proximity to end-users (farmers, dealers)
- Access to roads, electricity, and water
- Distance from residential areas (for odor control)
- Flat terrain, good drainage
Layout Zones:
- Raw material receiving yard
- Composting zone
- Crushing & mixing area
- Granulation, drying, and cooling line
- Screening and coating station
- Packaging and storage
- Office and utilities
4. Production Process Design
For a 20,000-ton/year capacity (~1,600–1,800 tons/month), the plant should handle 5–7 tons/hour during 1 shift of 8 hours per day.
Typical Organic Fertilizer Process Flow:
- Fermentation/Composting
- Crushing
- Mixing
- Granulating
- Drying and Cooling
- Screening
- Coating (optional)
- Packaging
5. Equipment Configuration for 20,000 TPA Line
Equipment | Model Suggestion | Capacity | Function |
---|---|---|---|
Compost Turner | Groove type or crawler type | 5–10 T/h | Ferments raw material aerobically |
Semi-wet Crusher | 40–60 kW model | 3–8 T/h | Crumbles fermented materials |
Mixer | Horizontal double-shaft mixer | 1–5 T/batch | Blends raw material and additives |
Granulator | New type organic granulator | 1–5 T/h | Forms powder into granules |
Rotary Dryer | Ø1.2×12m–Ø1.5×14m | 2–5 T/h | Dries moist granules to stable moisture |
Rotary Cooler | Matches dryer size | 2–5 T/h | Cools down dried granules |
Screening Machine | Rotary screener, 3–6 mm sieve | 2–5 T/h | Sorts granules by size |
Coating Machine (optional) | Small drum coating machine | 1–5 T/h | Adds anti-caking or nutrient coatings |
Packing Machine | Automatic, 20–50kg per bag | 3–6 bags/min | Weighs and packs finished fertilizer |
Conveyors | Belt conveyors, bucket elevators | Custom | Material transport throughout the plant |
Dust Collection | Cyclone, bag filter | Custom | Controls dust in crushing/drying zones |
6. Composting System Design
Type: Groove or windrow composting
Composting Cycle: 15–25 days depending on material and temperature
Key Inputs:
- Moisture: 50–65%
- C/N ratio: 25–30:1
- Oxygen: regular turning
- Optional: microbial inoculants for faster fermentation
Monitoring Parameters:
- Temperature: 55–65°C
- Odor: minimal
- Final moisture: <35%
Automation Options:
- Temperature sensors
- Automatic compost turners
- Aeration systems (for in-vessel composters) (Related post: organic fertilizer production project)
7. Granulation Line Details
Moisture of material before granulation: 30–35%
Preferred granulator:
- New Type Organic Fertilizer Granulator or
- Disc Granulator (if cost-saving is a priority)
Granule Size Control: 3–6 mm, adjustable by speed, angle, and moisture content.
Drying Target: Moisture reduced to 10–15% for storage and transport
8. Utilities and Auxiliary Systems
Electricity:
- Approx. 300–400 kWh/day, depending on automation level
Water:
- Mainly for composting and dust suppression
- 2–5 m³/day
Heating for Dryer:
- Biomass burner, gas-fired furnace, or steam boiler
- Thermal energy demand depends on raw material moisture
Dust and Odor Control:
- Bag dust collector in crusher/dryer
- Bio-filter system for odor from composting
9. Labor Requirement
Position | Number | Responsibilities |
---|---|---|
Plant Manager | 1 | Overall supervision |
Composting Operators | 2–3 | Turning, monitoring compost |
Equipment Operators | 3–4 | Crusher, mixer, granulator, dryer |
Packaging Workers | 2–3 | Bagging and stacking |
Maintenance & Electrician | 1–2 | Routine inspection and repair |
Quality Inspector | 1 | Final product testing |
Total Staff: ~10–15 persons per shift
10. Environmental Compliance
- Solid Waste: Utilize all organic material; minimal waste
- Wastewater: Minimal; compost leachate reused
- Air Emissions: Use dust collectors and deodorization systems
- Noise Control: Equipment with low-noise motors and enclosures
Certifications to Pursue:
- ISO 9001 (Quality Management)
- ISO 14001 (Environmental Management)
- CE Mark (for machinery exports)
- Organic Certification (for final product)
11. Budget Estimation
Cost Component | Estimated Range (USD) |
---|---|
Land and Construction | $100,000–$150,000 |
Equipment (Full Set) | $150,000–$300,000 |
Installation & Commissioning | $20,000–$50,000 |
Utilities & Accessories | $30,000–$50,000 |
Working Capital | $50,000–$100,000 |
Total Investment: $350,000–$650,000
ROI Period: 2–3 years (depending on fertilizer price and market demand)
Conclusion
Designing a 20,000-ton/year organic fertilizer production line requires careful planning, smart equipment selection, and systematic layout design. From raw material preprocessing to granulation, drying, screening, and packaging, each step must be optimized to ensure cost-efficiency and product quality. With the right setup and market strategy, such a plant can turn agricultural waste into high-value organic fertilizer while contributing to a more sustainable future.